Metal Fabrication: A Look Into the Technologies of the Future
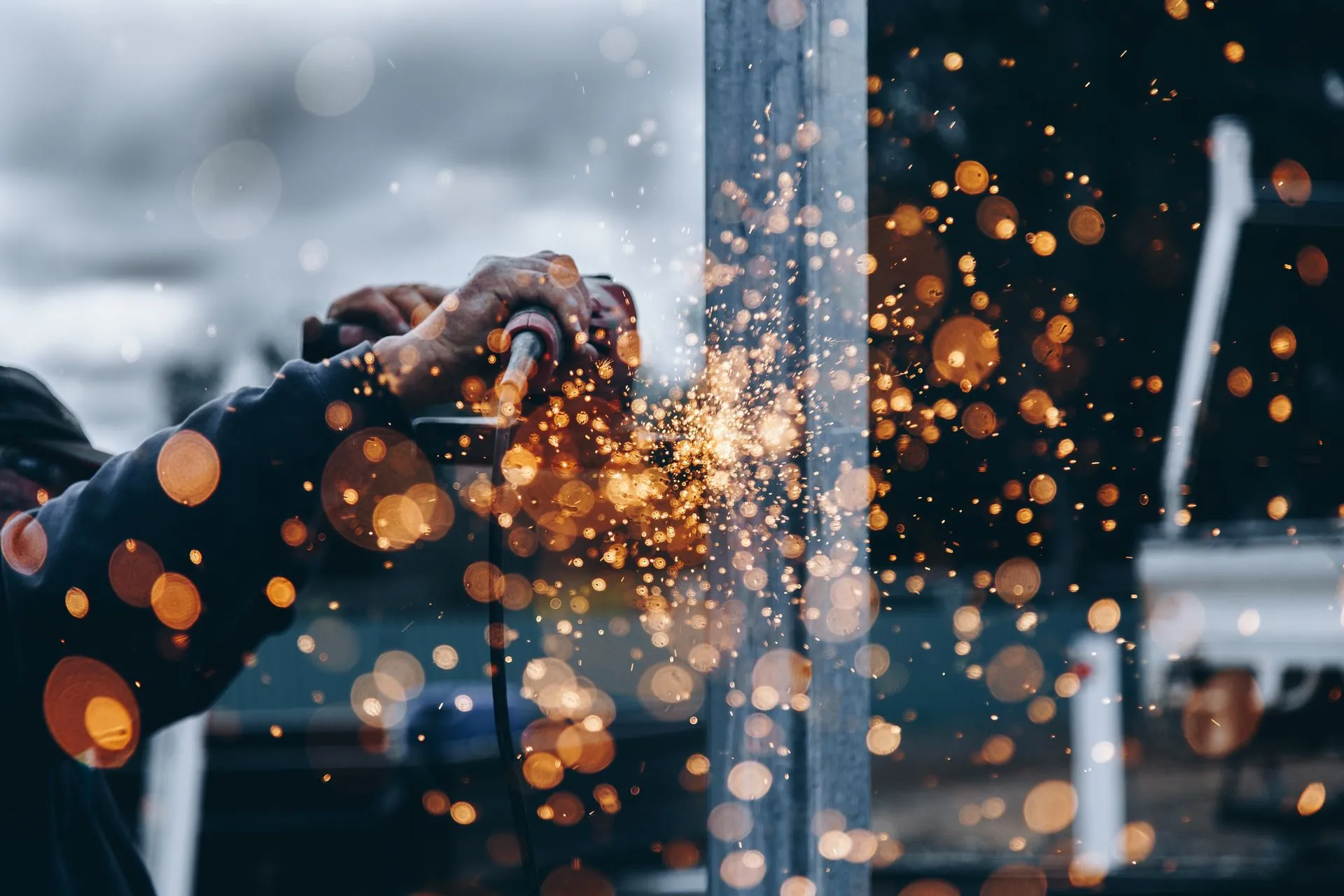
In the contemporary landscape of metal fabrication, the workshop is no longer a realm of traditional blacksmithing but a theater of technological marvels that command precision and efficiency. Among these, laser cutting and 3D printing take center stage, dazzling with a display that would leave seasoned craftsmen in awe. As we delve into the precision redefined by laser cutting and 3D printing, we uncover a transformative force that revolutionizes accuracy and reshapes the fabric of metal fabrication.
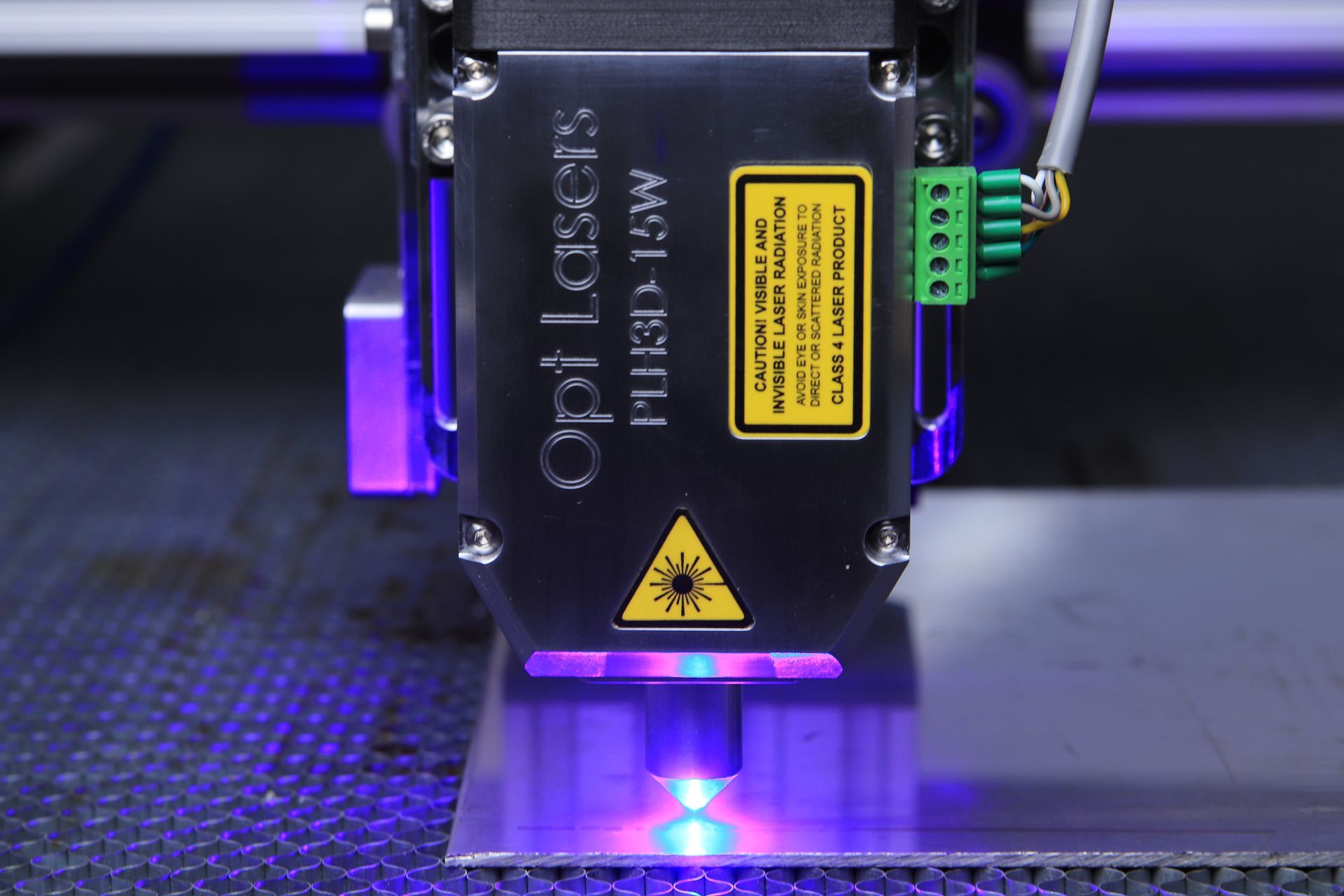
Laser Cutting: Precision Redefined
Enter today’s workshop, and you’ll likely witness a spectacle that leaves even the most seasoned blacksmith in awe—laser beams cutting through metal with surgical precision. Laser cutting has become the linchpin of modern metal fabrication, redefining the art of precision in ways once deemed unimaginable.
The power of laser cutting lies not only in its accuracy but also in its versatility. No longer confined to the limitations of traditional methods, laser cutting allows for intricate designs and complex geometries with minimal material waste. From crafting delicate patterns to navigating through thick sheets of metal, it can handle a spectrum of tasks with unparalleled accuracy.
The absence of physical contact between the cutting tool and the material ensures precision and mitigates wear and tear on equipment. This lack of mechanical abrasion translates into lower maintenance costs and prolonged machinery lifespan, making laser cutting not just a precise tool but a remarkably efficient one.
Material waste has become a concern of the past with laser cutting. The focused intensity of the laser beam means that cuts are clean, leaving minimal scrap behind. This contributes to environmental sustainability and aligns with the modern ethos of reducing waste in manufacturing processes. In an age where efficiency is synonymous with sustainability, laser cutting emerges as a key player in shaping the industry’s commitment to responsible practices.
Moreover, the speed at which laser cutting operates is a testament to its efficiency. Traditional methods often involve time-consuming processes that may lead to project delays. Laser cutting, on the other hand, completes tasks swiftly and accurately, reducing production timelines and increasing overall project efficiency. This newfound expediency is a game-changer, allowing manufacturers to meet tight deadlines without compromising precision.
In essence, laser cutting is not just a tool; it’s a transformative force that has redefined the fabric of metal fabrication. It has liberated designers and fabricators from the constraints of the past, unlocking a realm of possibilities where intricacy meets efficiency. As the laser beams continue to cut their way through not only metal but also the confines of the past, they illuminate a path toward a future where precision and productivity coalesce, shaping an industry as advanced as the beams themselves.
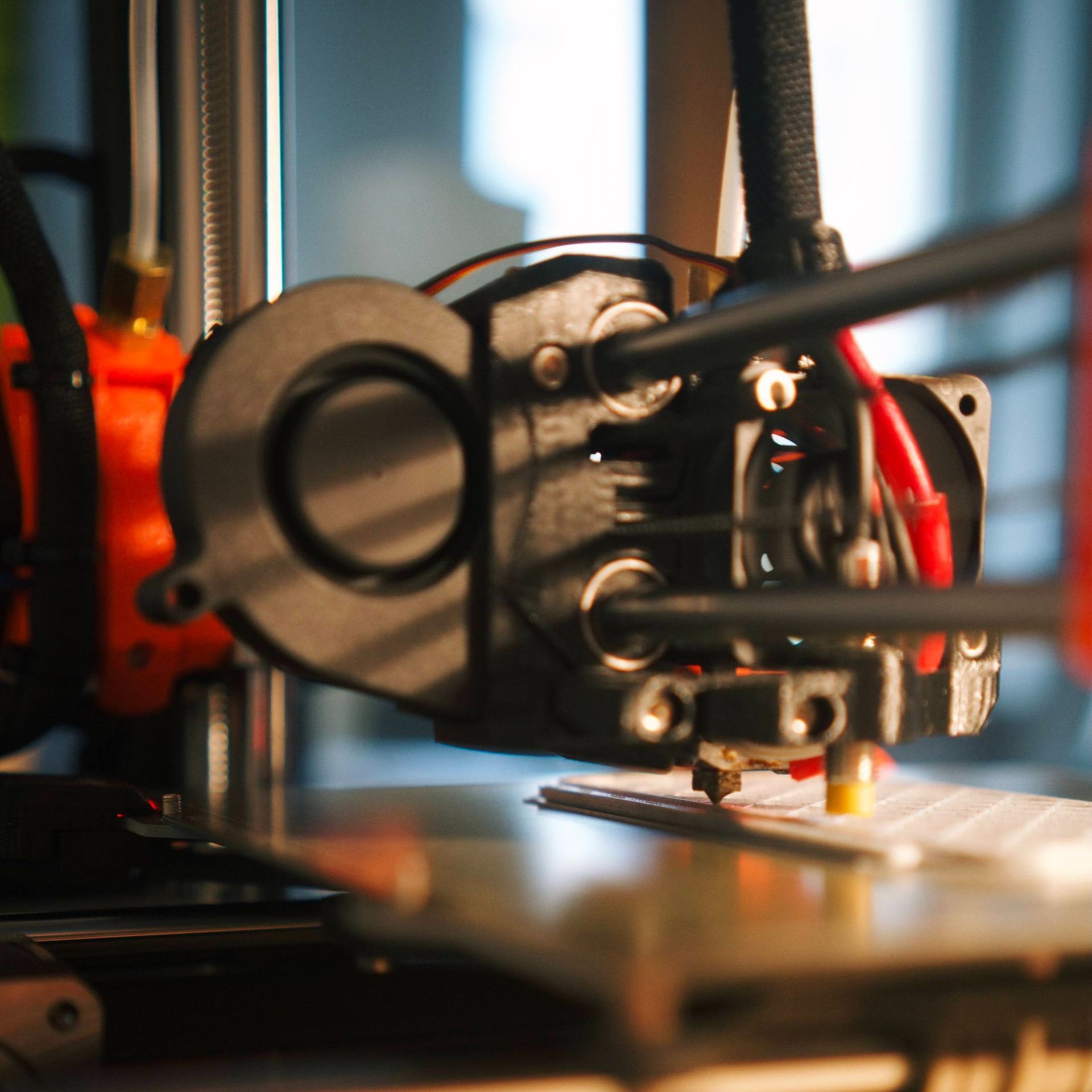
3D Printing: From Plastic to Metal Masterpieces
As we navigate the landscape of modern metal fabrication, 3D printing emerges as a transformative force, challenging the traditional norms and expanding the boundaries of what’s achievable. Initially celebrated for its prowess in the world of plastics, 3D printing has embarked on an audacious journey into the realm of metal, and the impact has been nothing short of revolutionary.
At the core of 3D printing’s allure lies its additive nature. Unlike traditional subtractive methods that remove material from a larger block, additive manufacturing builds an object layer by layer. This fundamental shift in approach minimizes material waste and introduces a level of design freedom previously unimaginable.
The applications of 3D printing in metal fabrication are as diverse as the designs it can bring to life. One of its standout features is the ability to create lightweight structures with intricate geometries. Traditional manufacturing methods often struggle with producing complex designs, but 3D printing effortlessly navigates the nuances, giving rise to robust and intricately detailed components.
The versatility of 3D printing extends beyond the manufacturing floor. Industries like aerospace and automotive, where lightweight yet strong components are paramount, have embraced this technology wholeheartedly. In the medical field, 3D printing has been a game-changer, enabling the production of customized implants and prosthetics with unmatched precision.
Furthermore, the cost-saving potential of 3D printing cannot be overstated. Additive manufacturing translates into significant economic benefits by minimizing material waste and allowing for intricate designs that require less post-processing. As the technology continues to mature, the financial advantages of 3D printing are becoming increasingly apparent, making it an attractive option for forward-thinking manufacturers.
The future of metal fabrication, as propelled by 3D printing, is not just about cutting or shaping; it’s about building. Layer by layer, additive manufacturing is ushering in a new era of design possibilities, redefining our understanding of what’s feasible in creating metal structures.
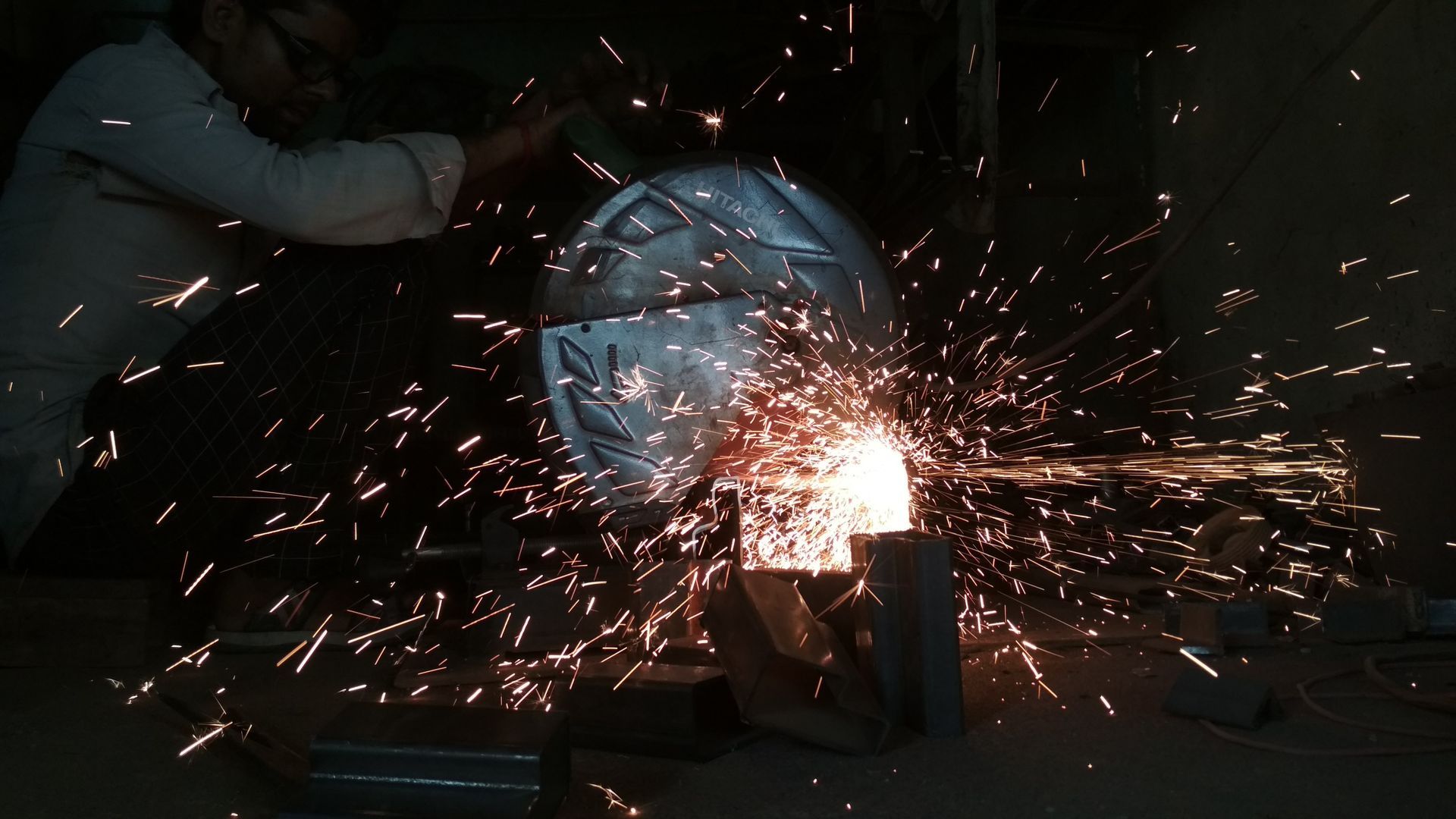
The ever-evolving saga of metal fabrication, laser cutting, and 3D printing stands as heralds of a new era. From the surgical precision of laser beams to the additive magic of layer-by-layer 3D printing, these technologies are not mere tools; they are transformative forces shaping an industry that refuses to be confined by the boundaries of the past. As we witness the convergence of precision and creativity, the future of metal fabrication unfolds with promises of efficiency, sustainability, and unparalleled design possibilities.
Newsletter
Don't miss a thing!
Sign up to receive daily news
Recent Posts
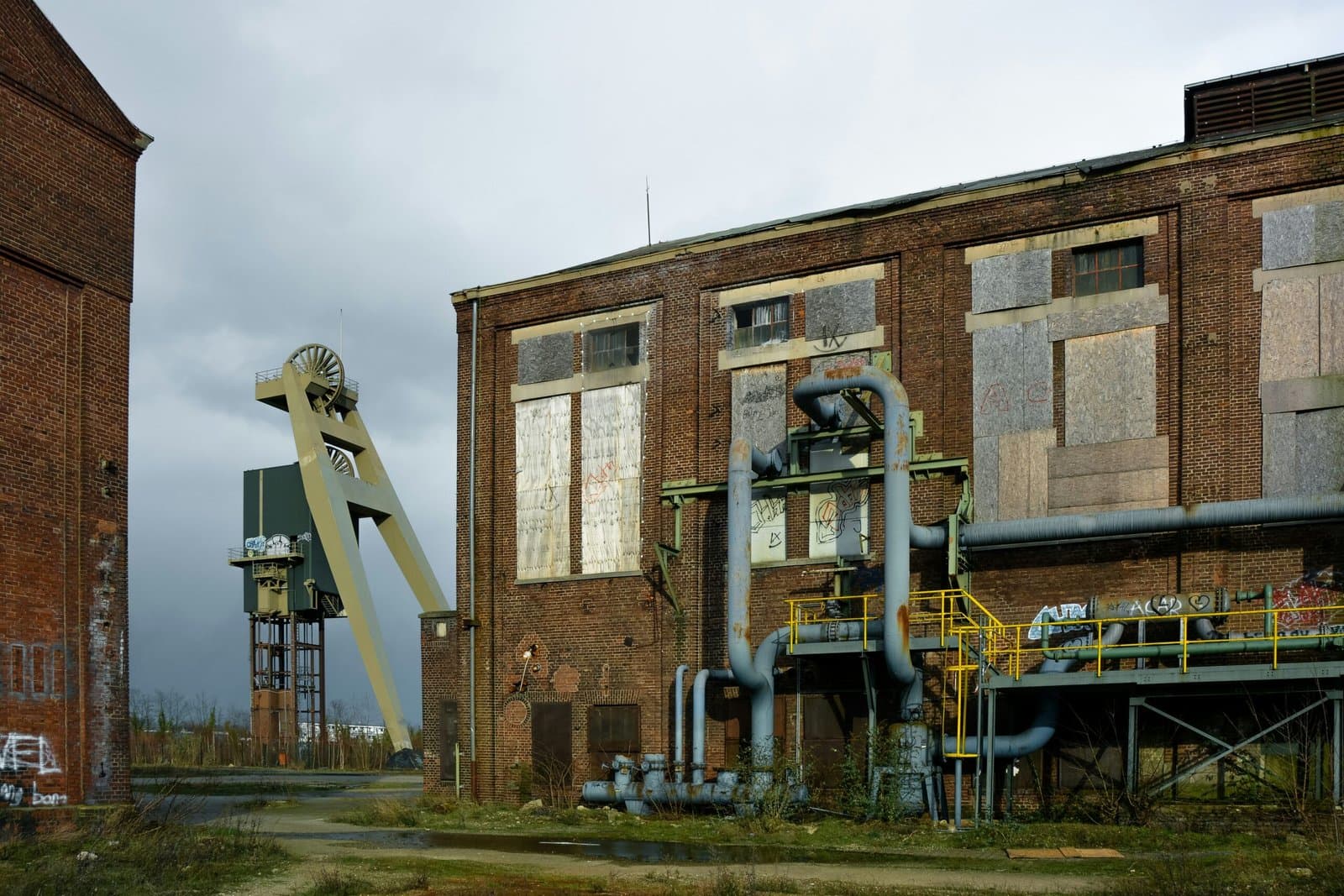
june 27, 2025
Turnkey Plant Relocation: What It Really Means
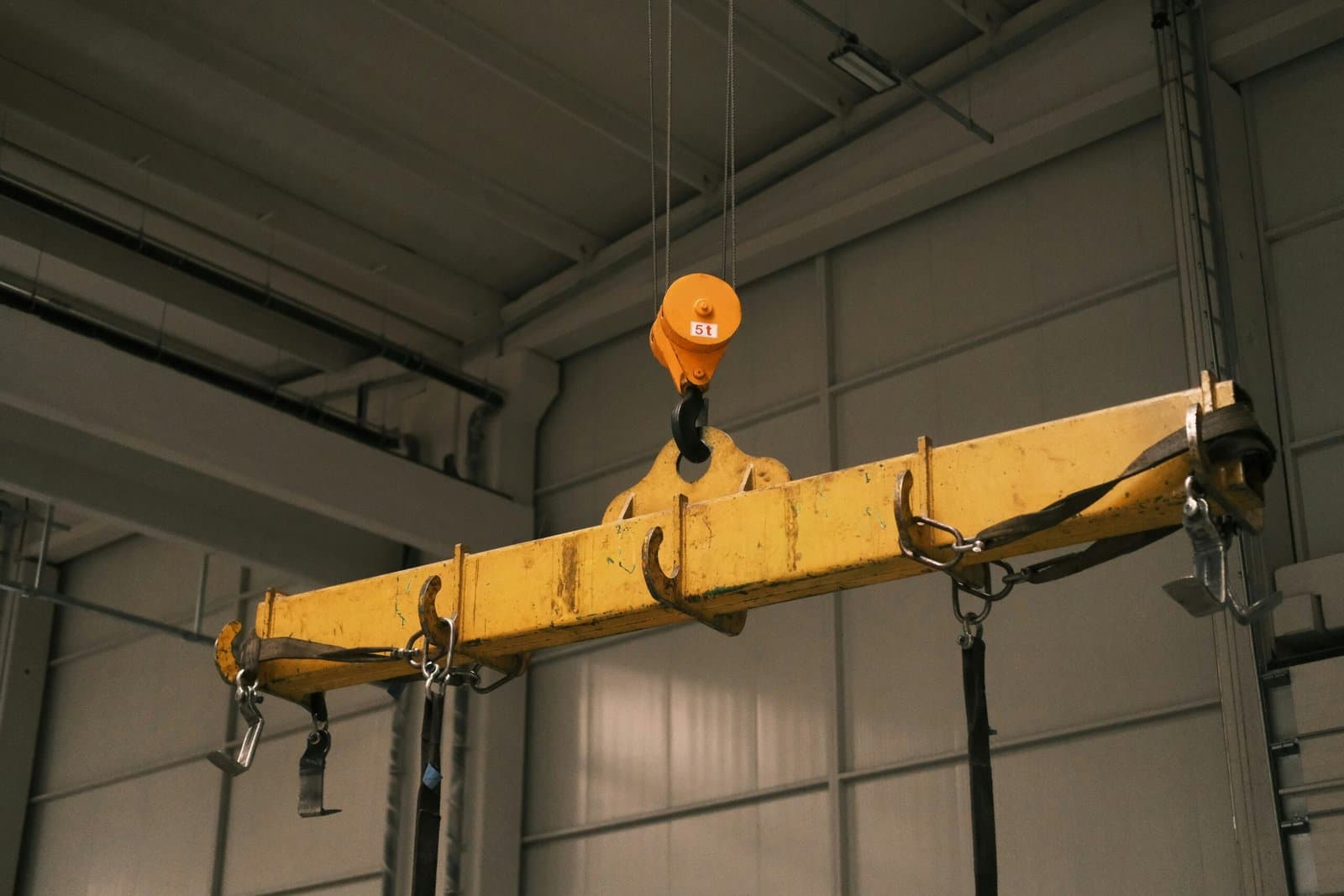
june 26, 2025
Industrial Machinery Rigging & The Hidden Dangers
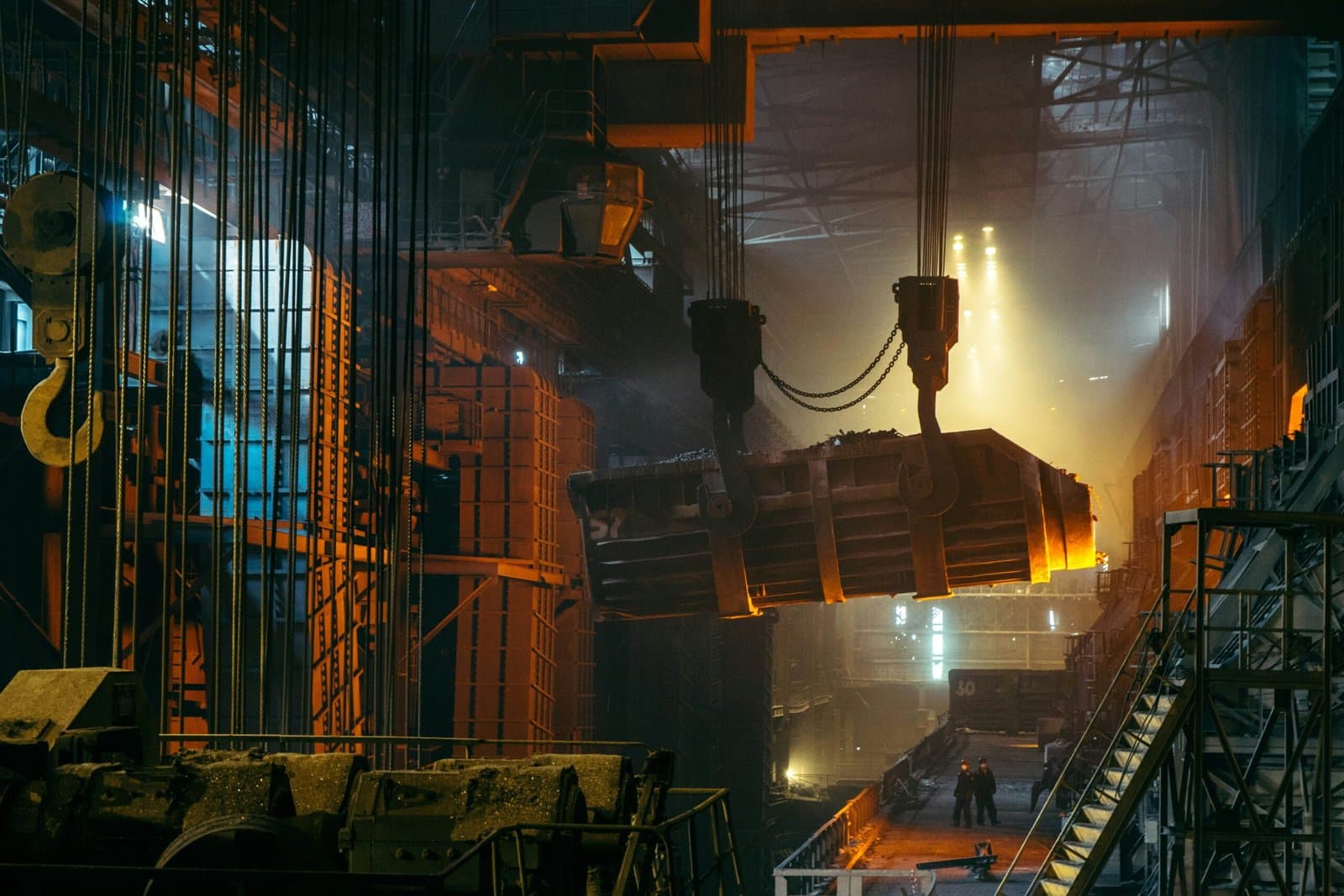
june 25, 2025
Industrial Machine Relocation: Essential Planning Steps
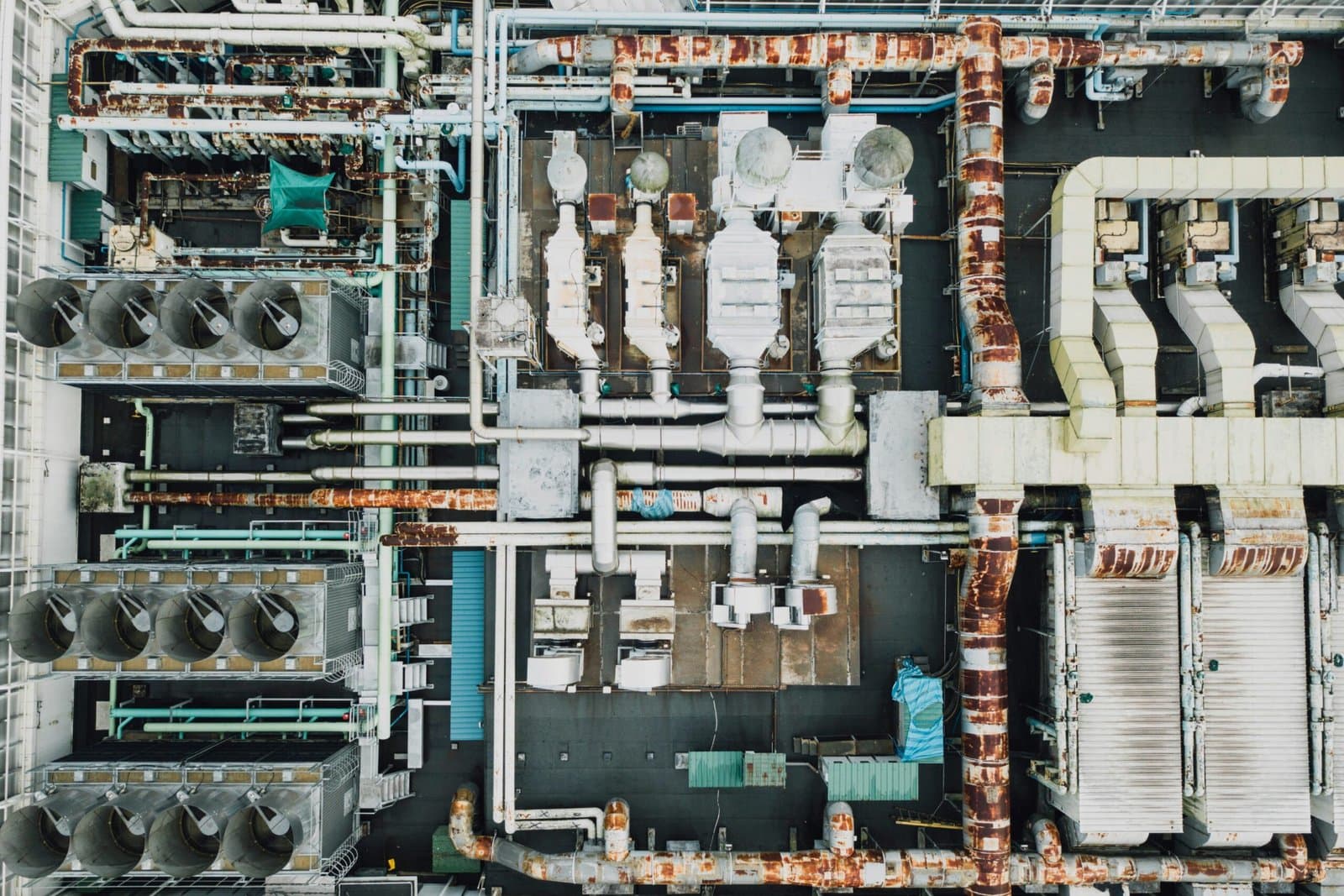
june 22, 2025
Industrial Relocation: A Strategic Move
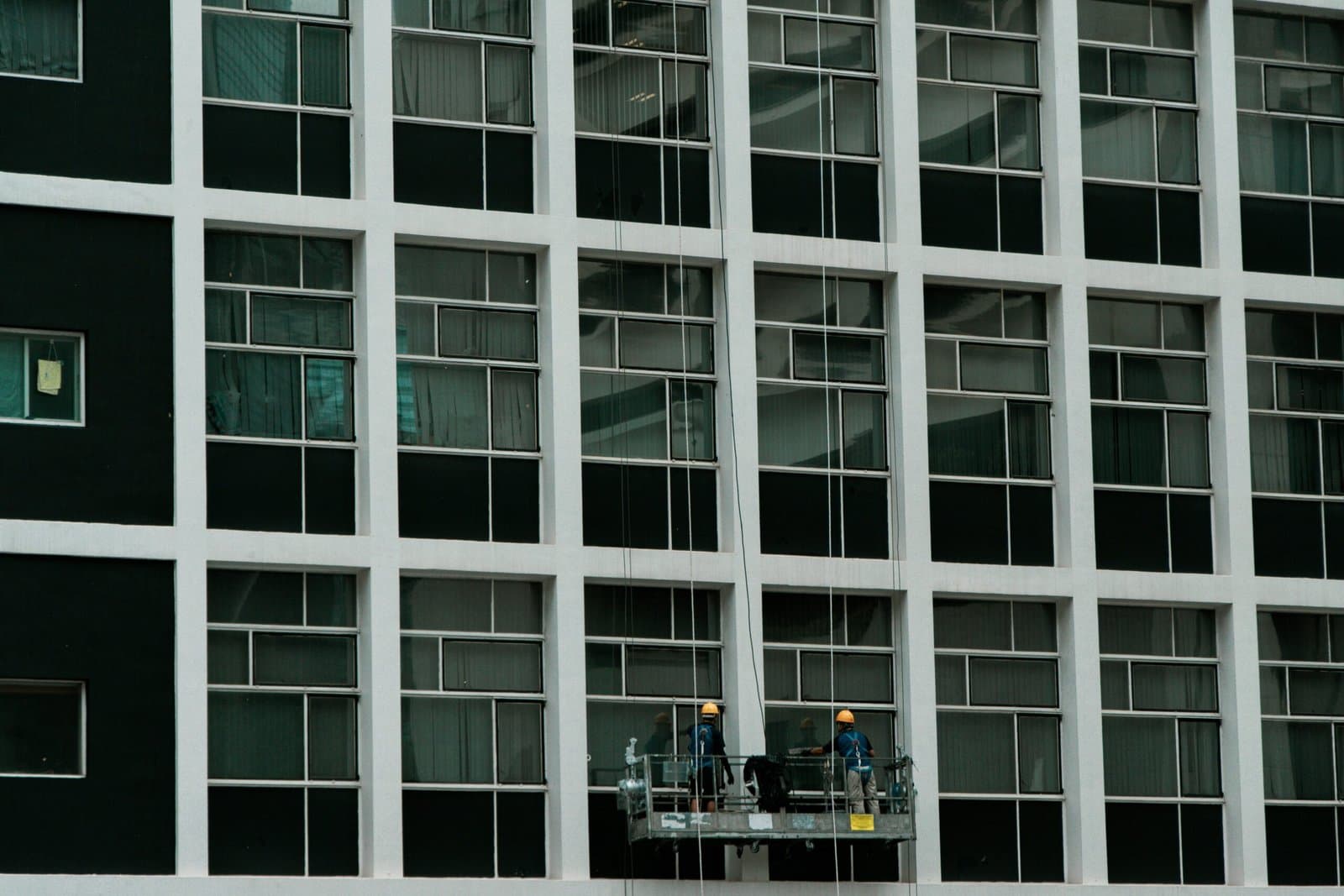
june 21, 2025
Post-Construction Window Cleaning
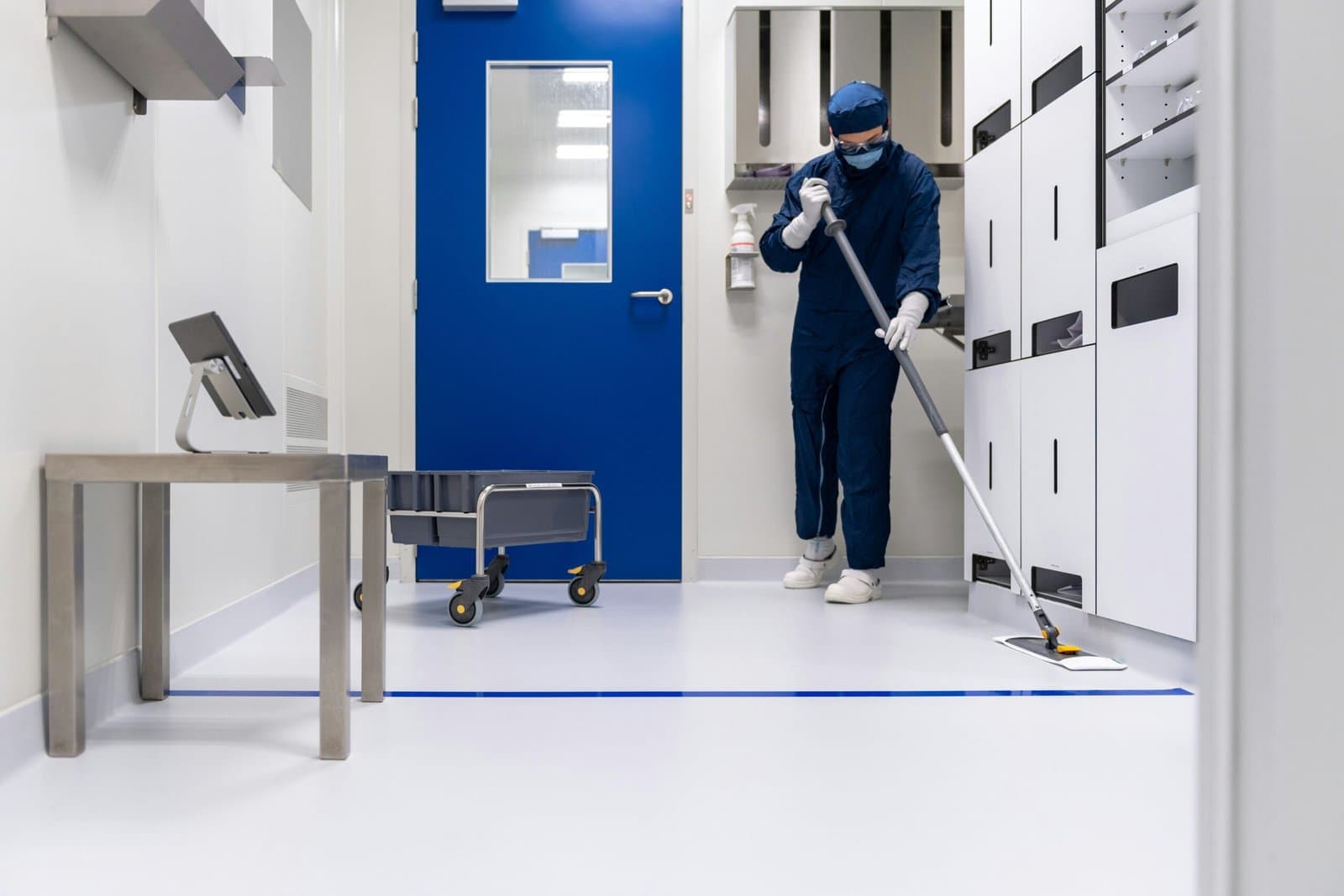
june 20, 2025