Industrial Fabrication: Transforming Raw Materials into Intricate Components
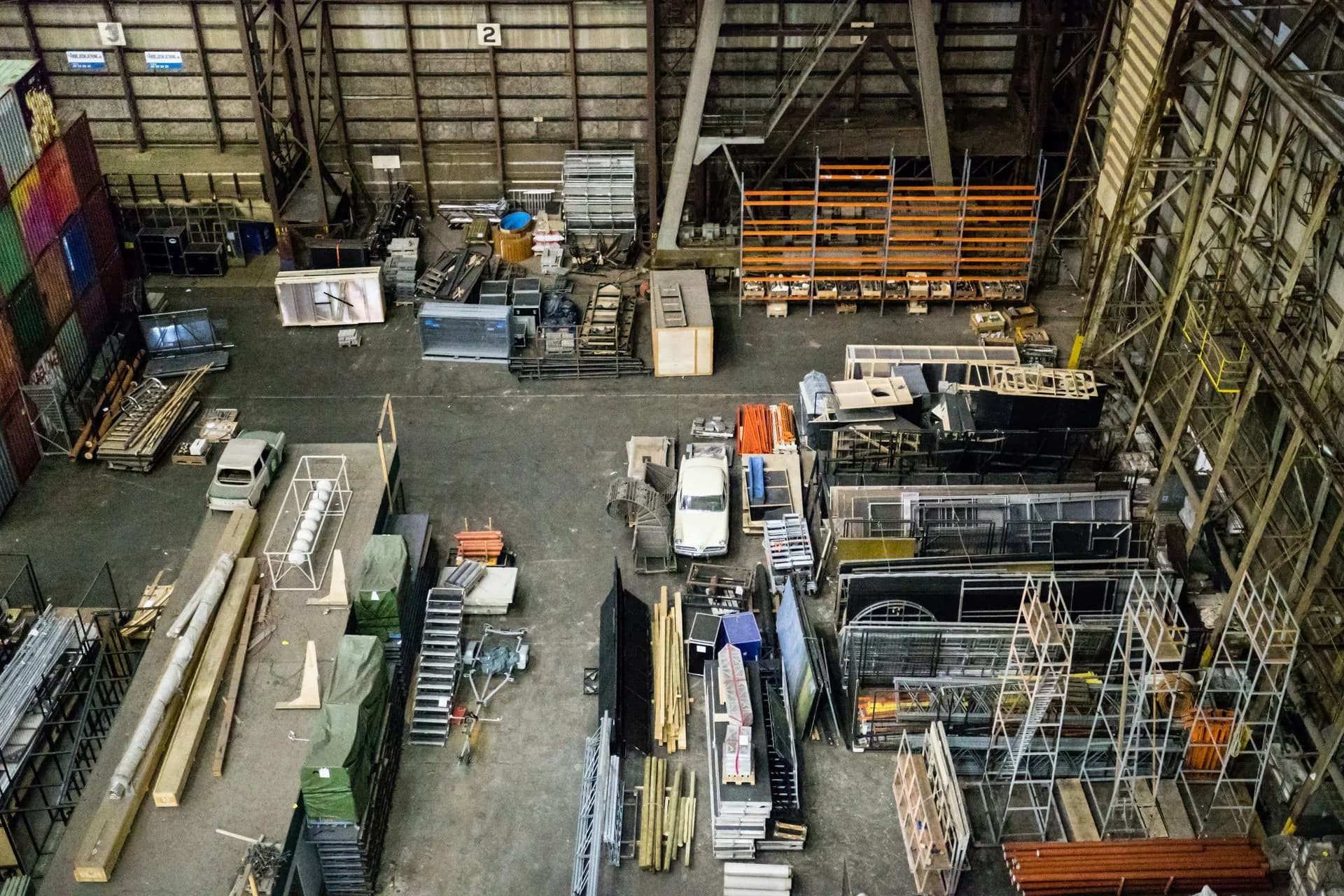
Industrial fabrication is a complex and fascinating process that plays a pivotal role in manufacturing various components used in various industries. From automotive parts to aerospace components, transforming raw materials into intricate and precisely engineered pieces involves a combination of advanced technologies, skilled craftsmanship, and innovative techniques. This blog post will delve into industrial fabrication, exploring the key steps in turning raw materials into the sophisticated components that power our modern world.
Selection of Raw Materials:
The journey of industrial fabrication begins with the careful selection of raw materials. Depending on the specific requirements of the component being produced, manufacturers choose materials such as metals, plastics, composites, or alloys. Factors such as strength, durability, and heat resistance are carefully considered during this stage to ensure that the final product meets the desired specifications.
Material Preparation:
Once the raw materials are selected, they undergo a series of preparation steps. This may include cutting, shaping, and refining the materials to achieve the desired size and form. Advanced technologies like laser cutting, water jet cutting, or precision machining are employed to ensure accuracy and consistency in the fabrication process.
Computer-Aided Design (CAD) and Prototyping:
In the modern era, computer-aided design (CAD) is crucial in industrial fabrication. Engineers use CAD software to create detailed 3D models of the components, allowing for precise planning and visualization of the final product. Prototyping further refines the design, enabling manufacturers to identify and address potential issues before mass production begins.
Fabrication Techniques:
The fabrication process involves various techniques, each tailored to the specific characteristics of the chosen materials. Standard methods include welding, forging, casting, and CNC machining. Welding joins metal pieces together, forging shapes materials through heat and pressure, casting creates intricate shapes using molds, and CNC machining employs computer-controlled tools for precision cutting and shaping.
Quality Control and Inspection:
Quality control is a critical aspect of industrial fabrication. Components are subjected to rigorous inspections to meet stringent quality standards throughout the process. Non-destructive testing methods, such as X-rays, ultrasonic testing, and magnetic particle inspection, are commonly employed to detect any defects or imperfections that could compromise the integrity of the final product.
Finishing and Surface Treatment:
After the fabrication, components often undergo finishing processes to enhance their appearance and functionality. Surface treatments like painting, coating, or polishing may be applied to improve corrosion resistance, provide aesthetic appeal, or meet specific industry standards.
Industrial fabrication is a blend of art and science, where skilled craftsmanship and cutting-edge technologies transform raw materials into intricate and high-precision components. As industries continue to advance, so will the techniques and processes involved in this fascinating field, shaping the future of manufacturing and innovation.The body content of your post goes here. To edit this text, click on it and delete this default text and start typing your own or paste your own from a different source.
Newsletter
Don't miss a thing!
Sign up to receive daily news
Recent Posts
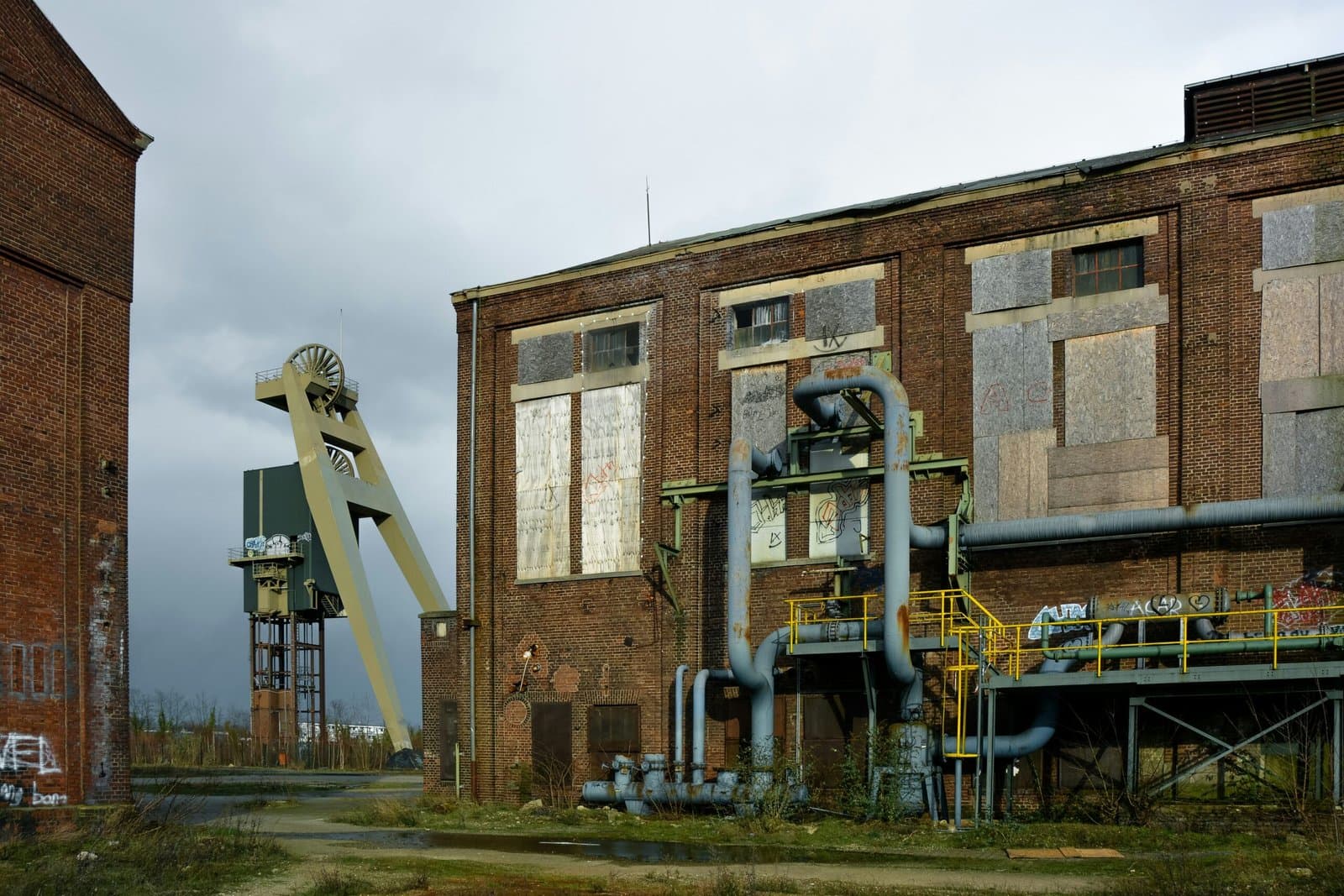
june 27, 2025
Turnkey Plant Relocation: What It Really Means
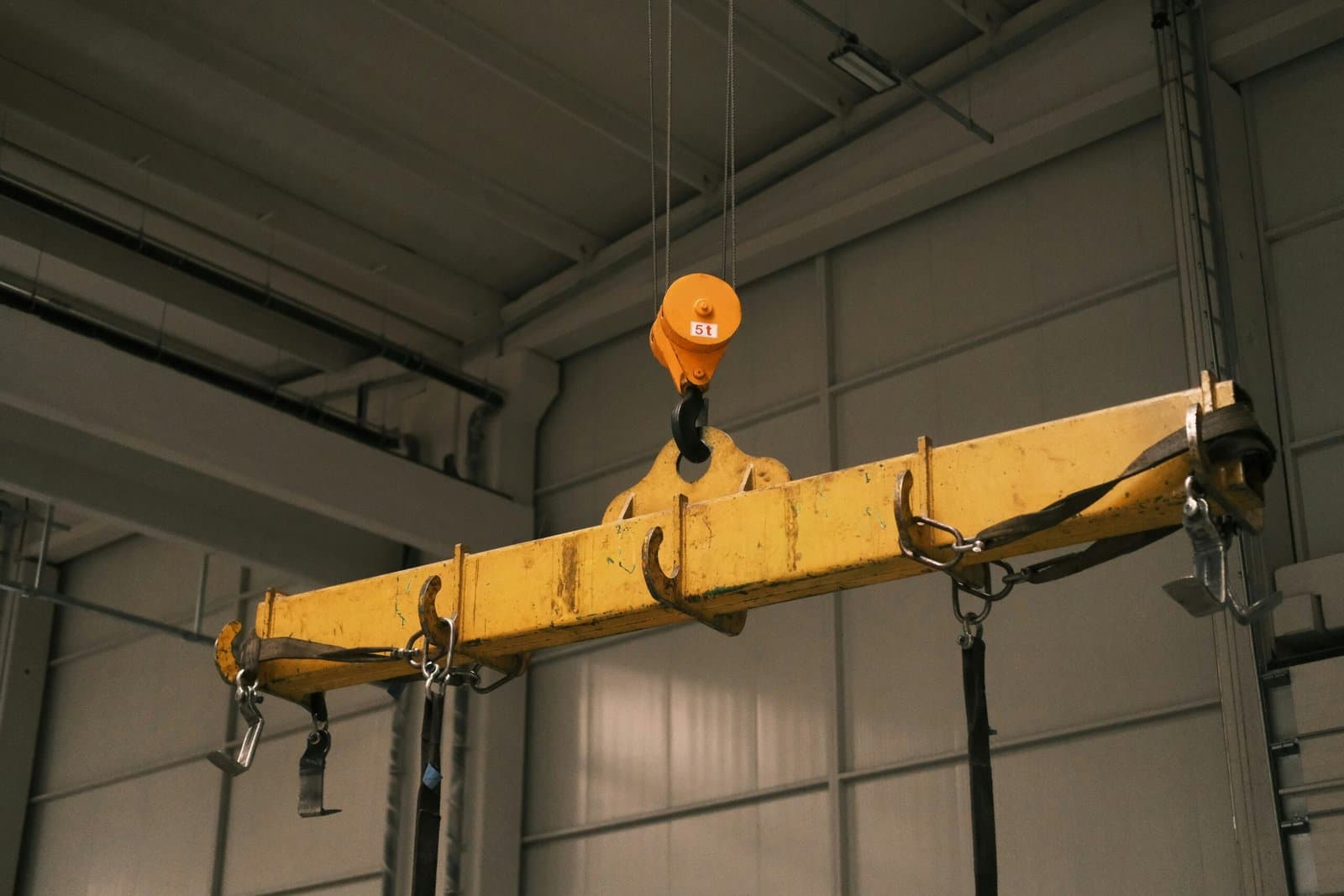
june 26, 2025
Industrial Machinery Rigging & The Hidden Dangers
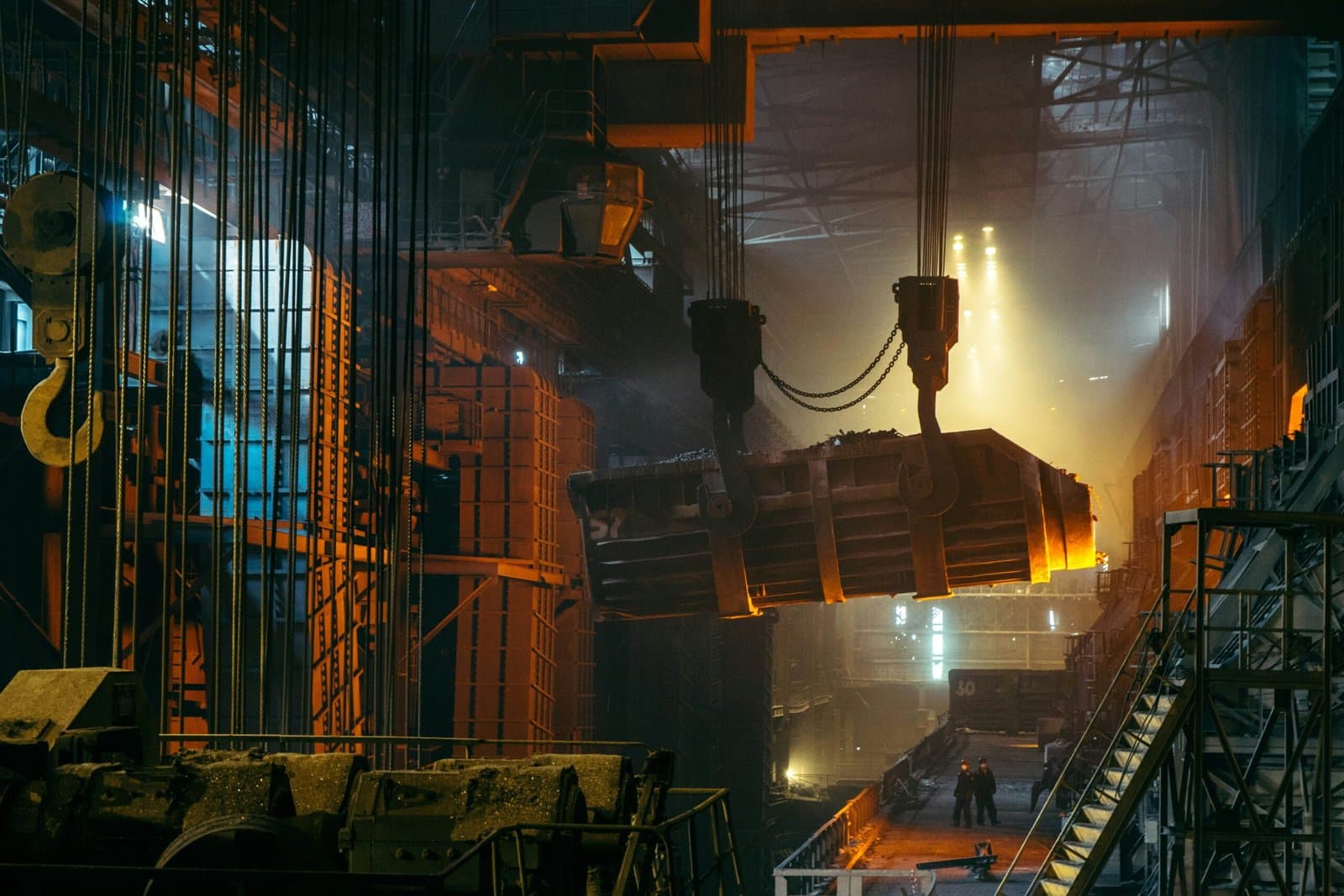
june 25, 2025
Industrial Machine Relocation: Essential Planning Steps
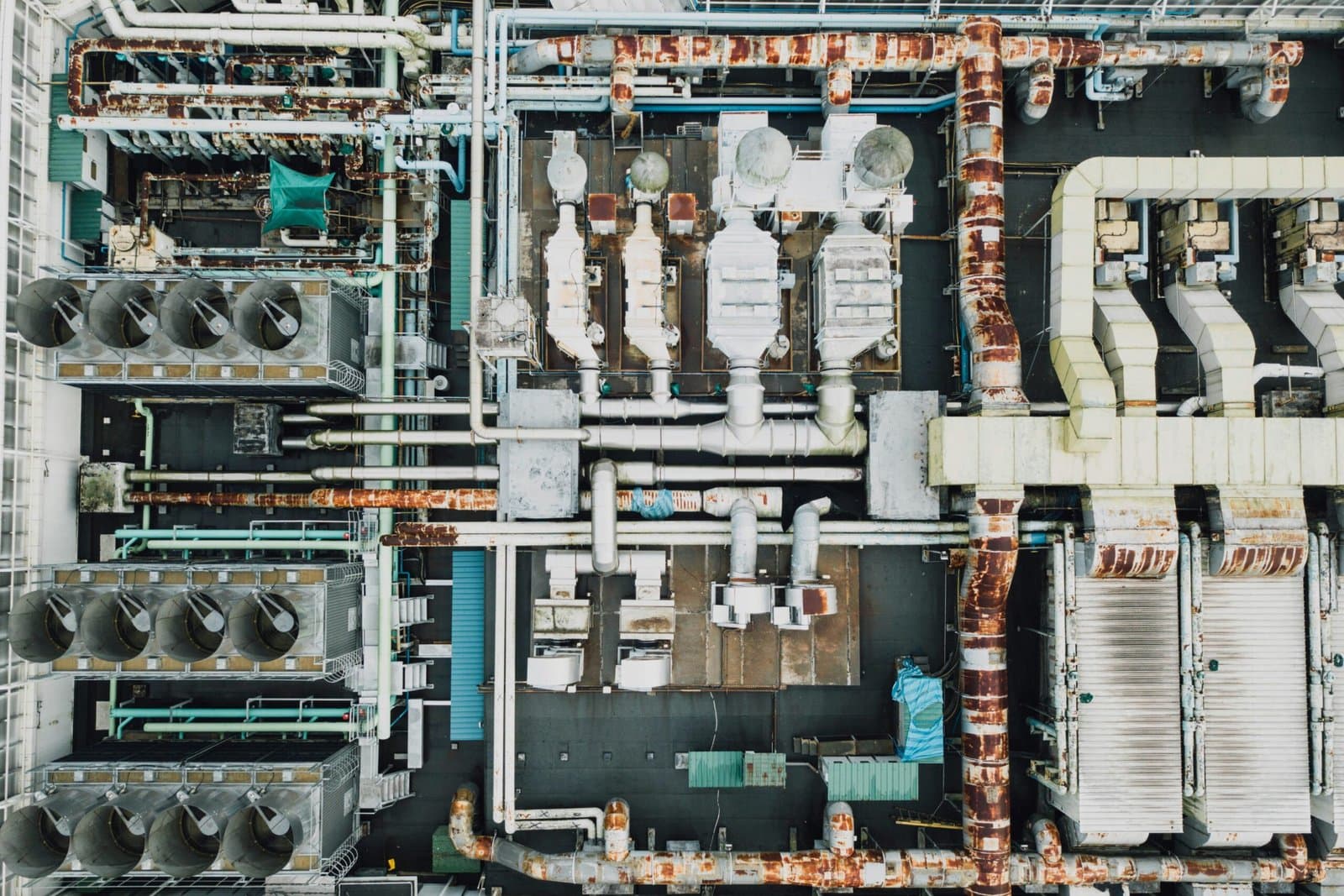
june 22, 2025
Industrial Relocation: A Strategic Move
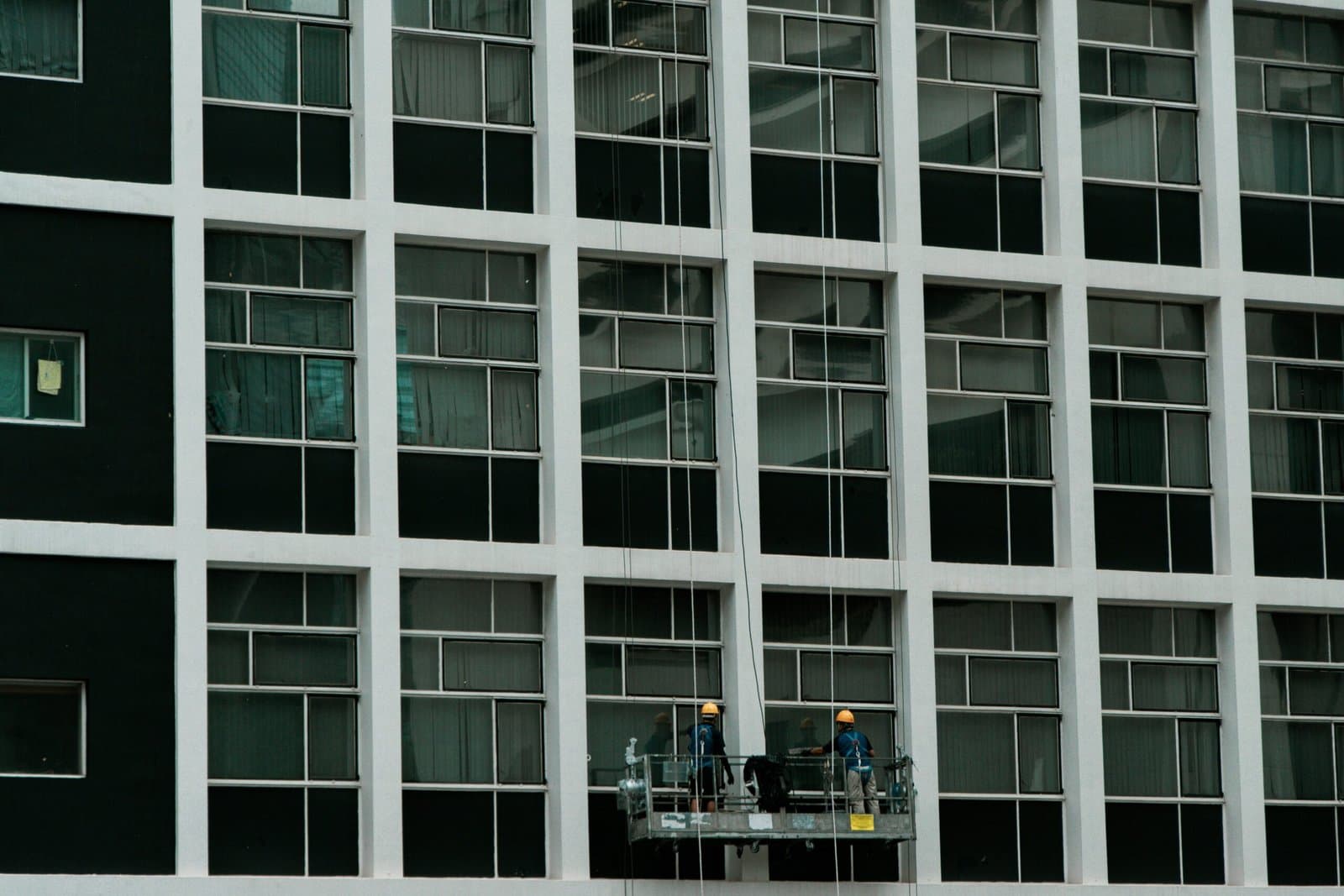
june 21, 2025
Post-Construction Window Cleaning
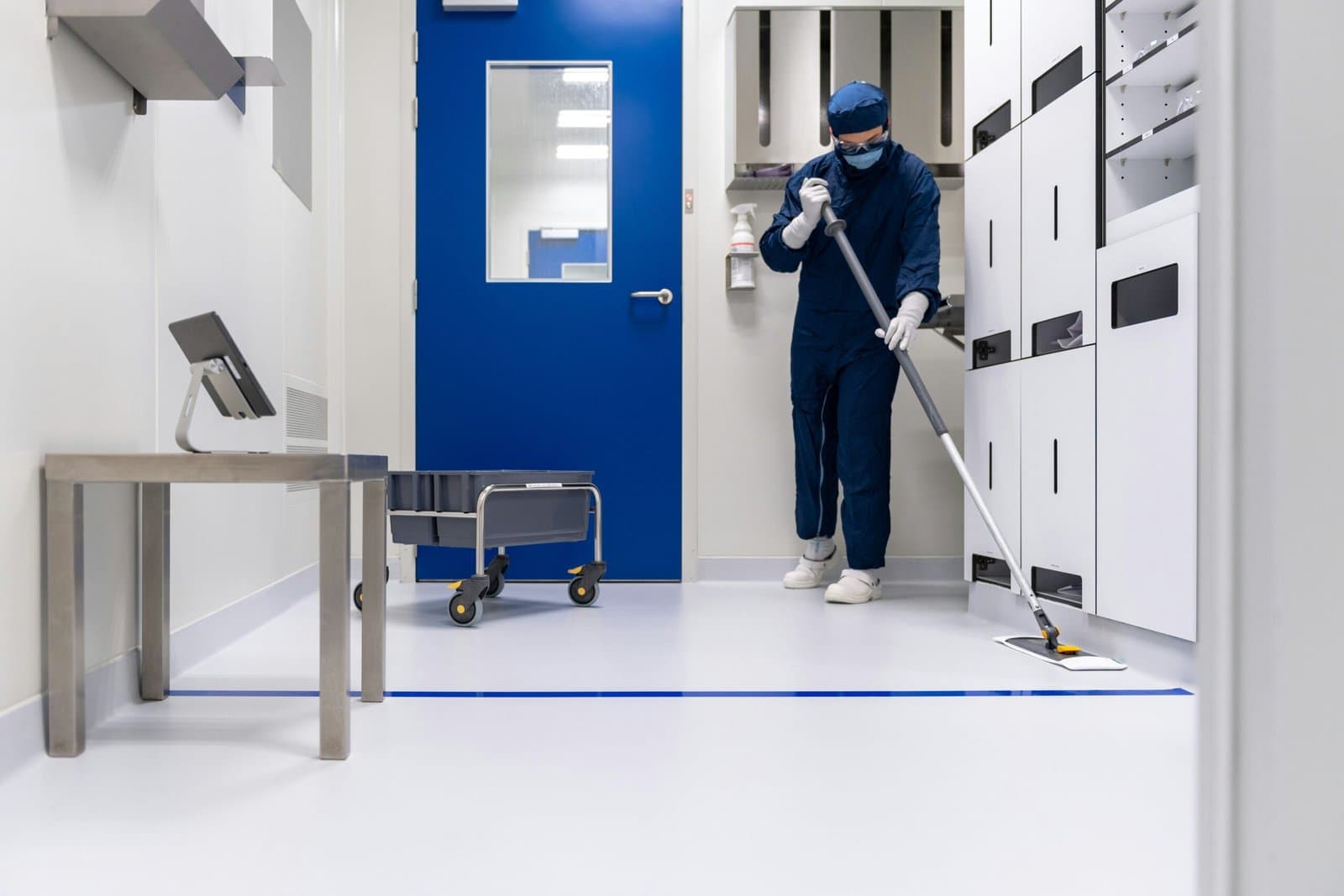
june 20, 2025